Searching for the right Celadon glaze: part 1
- Micaela
- Jul 13, 2017
- 3 min read
As part of my research into the decorations for my next set of larger figures I've started to mix and test different celadon glazes.
A celadon glaze is a traditional greenish stoneware glaze produced in China, Korea, Thailand and Japan. The earliest celadon pottery, Yue ware, was produced in China during the Han dynasty (206BCE-220CE) and was olive or a brownish green colour. With the innovation of different kiln technology which offered much more controlled reduction processes the glaze colours changed to much cleaner and brighter greens. Celadon glazed pots were particularly valued in China because of its strong resemblance to Jade. During the Song dynasty (960-1279) the first Chinese celadon pottery made it into Europe. Considered the pinnacle of Chinese pottery production however was during the Ming dynasty (1368-1644). Decorations were very often created by carving patterns into greenware or even using moulds with patterns.
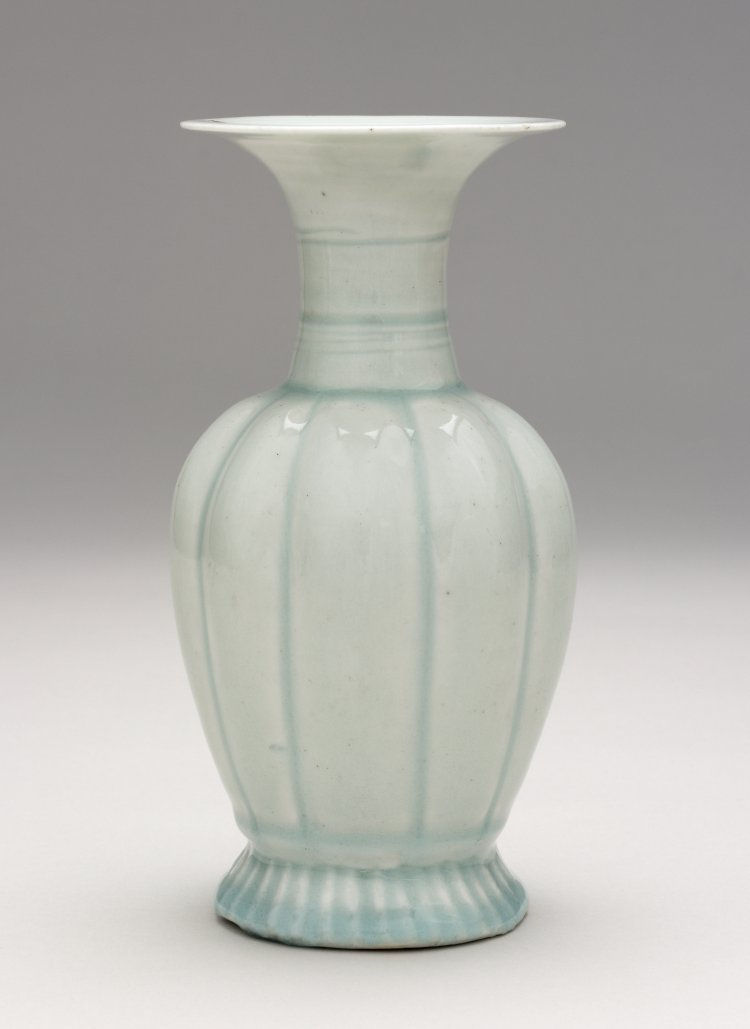
Top: 12th century Song dynasty vase
Bottom: 1517 Ming incense-burner
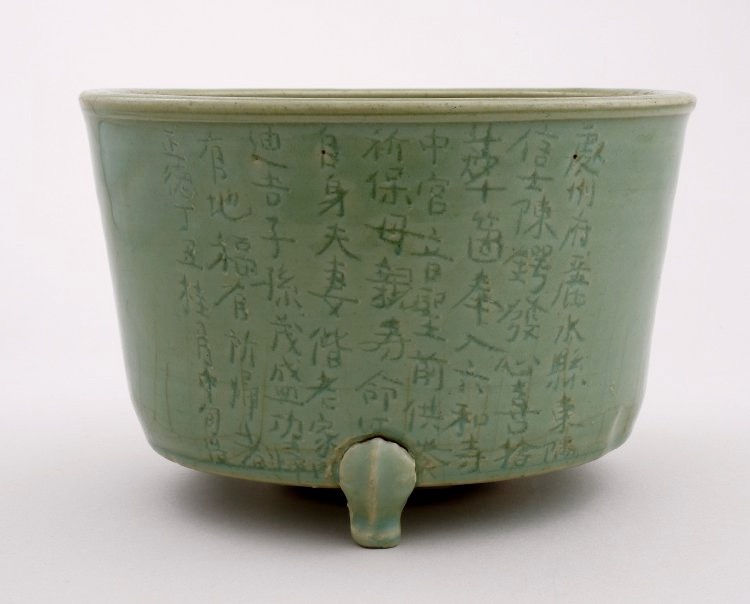
However, celadon glazed porcelain production spread to other neighbouring countries, who produced their own versions. The hight of Korean celadon pottery was during the Goryeo (or koryo) dynasty (918-1392) and had a strong Bhuddist influence. Korean potters perfected the use of inlay and copper glazing techniques of their celadon ware. Much of this knowledge was lost after the Mongol invasions, which began in 1231.


Both Goryeo ceramics are from the 12th century.
Strangely enough I didn't find much on historical Japanese celadon ceramics. Apparently Japan had a large variety of different ceramic styles, much more than its neighbours, but had limited amount of some of the key resources needed to make celadon ceramics. This combined with an 80% failure rate may account for this. Or I've just looked in the wrong direction.

Celadon pottery production lasted in Thailand from the 13th century to the 16th and is know also as Sukhothai or Sawankhalok ware.
Deep circular bowl with floral rim 15th century, Thailand.
My idea is to have a set of figures that reference traditional historical ceramics but with my own personal twist. For my previous set used strong graphic elements created by using underglazes. This time I am planning to keep my figures much more monochrome with a limited use of underglazes as part of creating texture which is brought out by the use of a glaze.
Firstly, I have been looking at four different recipes each of which contain 2% red iron oxide and needs to be fired in reduction.

I started off with the celadon glaze that is ready mixed in the studio. I have previously tried it out on quite a few clay bodies but even on a very white bodied clay PF700G Porcelain White S/Ware Grog it lacks the bright aqua quality I'm after.

After mixing another celadon glaze and testing it on a different clay body, in this case B17C I realised that I needed to approach this much more systematic in order to have comparative samples that could lead me to what I want.
Thus decided to make a set of test tiles which would not have any decorations except for incised grooves. I began with different three celadon glazes on two different clay bodies.

The top row is the very white PF700G clay and the bottom Ashraf Hanna clay. On the left is a clear s/w glaze I found in Jo Connel's book "The Potter's Guide to Ceramic Surfaces. To this I thought I try adding 2% red iron oxide. The middle is a celadon glaze I found in the same book. And the glaze on the right is one that Geoff, our studio technician, had in his personal collection of glazes. As it turns out this was the most successful of all the three tested so far. All tiles were fired to ca 1265°c in reduction.
However, before delving further into more true celadon glazes Dave during my tutorial suggested that I'd look into finding a fake or faux celadon glaze that didn't rely on access to a gas kiln, which I was unlikely to have after finishing the course. That made total sense as my aim is not the be a purist but merely to allude to a historical visual vocabulary, i.e. for my pieces to 'look a bit like' the original.
Comments